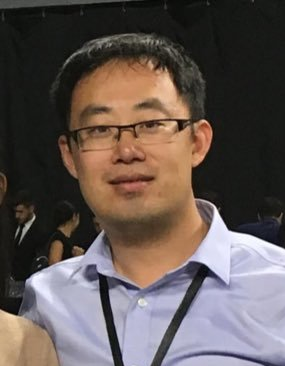
Professor Hao Su
Cybernetic biological augmentation, an idea popularized by DC Comics, and Bungie, Inc. is no longer an unobtainable goal, relegated only to the realm of science fiction. Step-by-step, Mechanical Engineering Professor Hao Su helps walk the world into the robotic future.
“In my lab we work on wearable robots, in particular, soft, wearable robots. The general goal is to design robots that can be attached to human limbs, like a modular hip exoskeleton or modular knee exoskeleton, to improve mobility for both able-bodied individuals and people with disabilities.”
The team at the Biomechatronics and Intelligent Robotics (BIRO) Lab, is able to design motors that are unprecedentedly lightweight without compromising their ability to generate the high levels of torque necessary to facilitate human locomotion. “If you think about the smartphone, 30 or 40 years ago, they were not mobile phones. We are making this paradigm shift from tethered,” asserts Su, emphasizing the utility of battery-powered, portable devices.
You can imagine that a mechanical exoskeleton would be rigid and hard to move, but through the use of novel types of sensors, actuators and sophisticated artificial intelligence algorithms, the BIRO team has developed robots that are highly responsive to the wearer’s movement cues. “Whatever you do, whether you are walking, squatting, or running, the robot will be able to synchronize with the movement, to maximize human performance,” he says.
Collaborators at the National Institute of Health (NIH) Clinical Center, Columbia University Medical Center, University of Texas Health Science Center at Houston, TIRR Memorial Hermann Hospital, and Mount Sinai’s Icahn School of Medicine provide Dr. Su’s team with opportunities to bring their innovations to the real world. These medical sites enable patients who suffer from musculoskeletal injuries, neurological disorders, and/or other types of impairments, to try on the wearable robots their lab develops. Such translational collaborations facilitate mutually beneficial interactions between patients and STEM professionals. Patients regain a tremendous deal of mobility and independence, while researchers quantitate the germane parameters useful to improving the design of the robotic technologies.
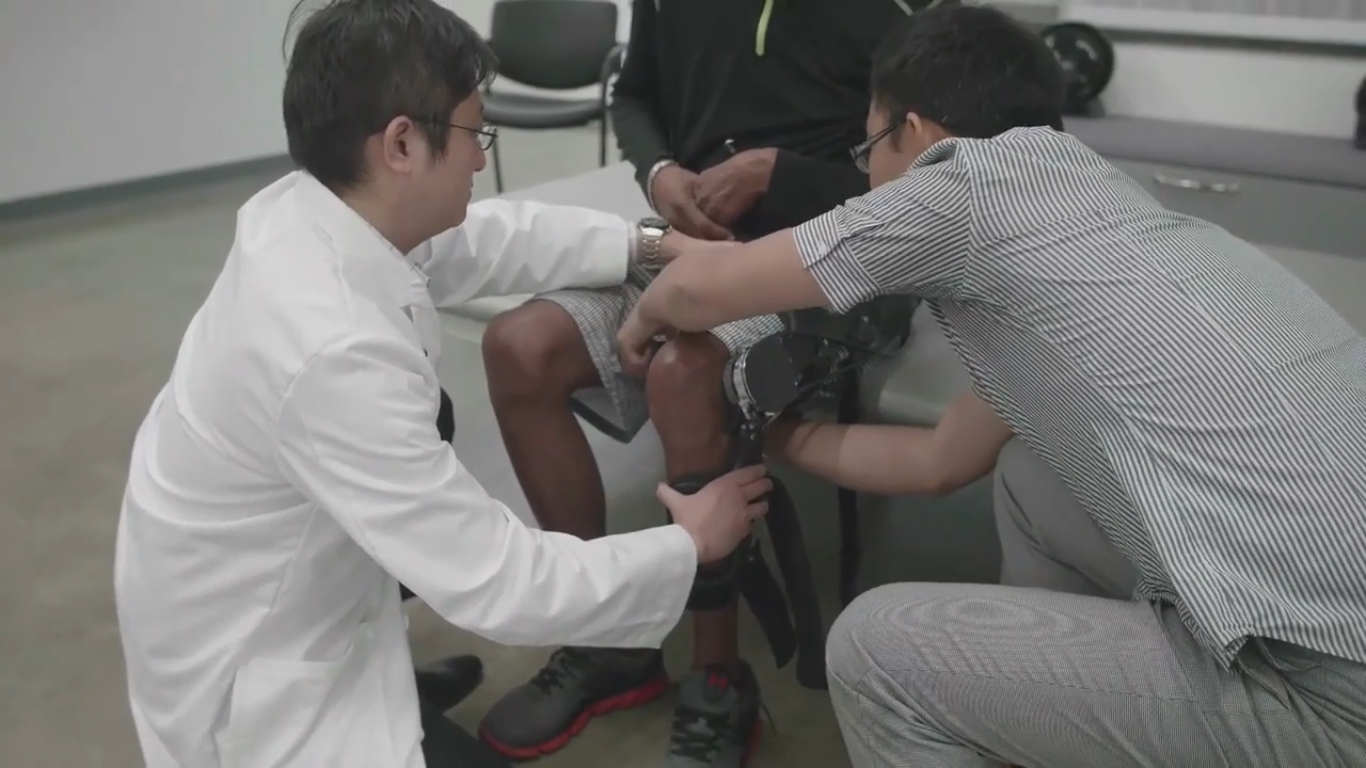
A knee exoskeleton, 3D-printed based off of a three-dimensional scan of the patient’s leg, being applied for testing
Another fundamental goal of the BIRO Lab is to make robotic interventions more affordable. “To reduce production costs, we’ve developed an integrated actuator instead of purchasing components from different vendors. We also have developed our own control electronics instead of using commercially available components. Overall, the material cost of each exoskeleton leg is about $3,500, and the labor and development costs total about $15,000 per leg. “Our robot is about 50% cheaper than state-of-the-art robots,”
Dr. Su emphasizes that this is not only for those who have neurological impairments. Wearable robots are also beneficial for able-bodied people. A worker gets injured every 7 seconds, and the most common injuries are muscle sprains, strains, and tears. In the future, he hopes that robots can decrease these statistics.
Dr. Su’s research is not limited to only biomechatronics; it additionally encompasses, surgical robotics and how robots can be utilized to combat infectious diseases.
Recently published papers in Nature Machine Learning, and in Science Robotics, explores how robotics can be used to combat the current COVID-19 pandemic. The glove-like robotic hand exoskeleton was developed for people who have suffered a stroke, this experience is being utilized to develop a portable gripper that can be used in laboratory settings where SARS-CoV-2 is handled. The grippers are far stronger than pre-existing conventional technologies as published in Science Advances.
“Our robot can generate much more force than traditional robots. The cool part is, it can lift very heavy objects – up to 20 pounds. Most grippers are bulky and can only lift about one or two pounds, so our gripper is very powerful.”
“Humans are not very good at precision,” he says, “They are not a precise robot.” Even veteran microsurgeons aren’t exempt from the sub-clinical tremors we all have from our motor neurons’ incessant action potential firing. To circumvent this, Professor Su’s team, in collaboration with Harvard Medical School, has developed a robot that assists in prostate interventions. He additionally has worked in collaboration with John Hopkins University, and Brigham and Women’s Hospital to developed master-slave telesurgery robots for MRI-guided robotic neurosurgery.
In recognition of his outstanding work, Dr. Su received a $2.78 million National Science Foundation (NSF) grant to support the development of Perceptive and Adaptive Soft (PECASO) Robots. With this funding, he will lead an 8-person team composed of faculty from CUNY, New York University, and Rutgers. In 2020, he additionally received an NSF CAREER award, providing him with $552K to march along the Human-Technology Frontier.
Dr. Su is passionate about recruiting young minds to STEM and robotics. He has worked with students from every rung on the academic ladder. Every summer, he mentors three high schools, and three undergraduate students. Sometimes this trickles over into the regular semester. With him, they have 12 published conference and journal papers and have won 2nd and 3rd place prizes in international competitions.
“Something I really want to share is that I would encourage students to get involved in STEM majors, in particular, medical robotics areas, because they’ll learn a very interesting topic. And also, after they graduate, they probably can find a very good job at Apple or Google, because they have an interest in those domains. Robotics is really, I think, the next big thing, and I really want to have more students work with me.”